Ways to create a factory that is more INTELLIGENT
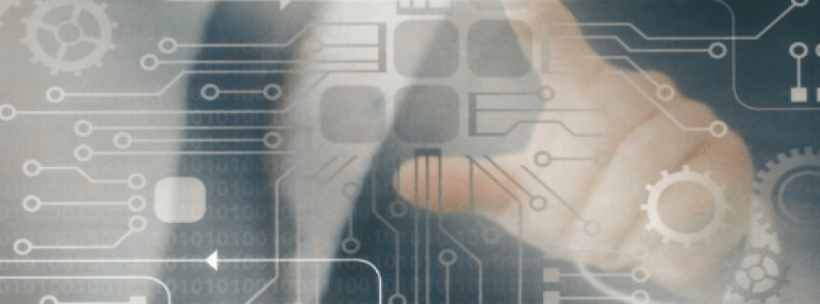
The production of food and beverages is changing at great speed and is becoming increasingly demanding. This can only be achieved by ensuring a greater optimization of assets, thus satisfying the growing demand for healthy, convenient, sustainable and differentiated products. - SIG
Supplier of systems and solutions for aseptic packaging / [email protected].
As factories and filling plants operate on an unprecedented scale, production lines must be more flexible, individualized and digital in order to handle periods of higher production and faster product changes.
This can only be achieved by ensuring a greater optimization of assets, configuring the optimal infrastructure in the long term that can handle any operational demand in a flexible way and guaranteeing an intelligent planning of production, recipe and organization of work throughout the production.
Danyoush Sangi, Head of Production Engineering & Strategic Alliances at SK3, shares his vision on how to create a smarter factory and navigate in the era of Industria 4.0.
-What do you think are the biggest challenges for food and beverage manufacturers today?-
The future of food and beverage production is to satisfy a growing demand for healthy, convenient products that are safe, sustainable, insurable and differentiated. All companies are under increasing pressure to increase production, improve margins and optimize assets. Filling plants must be smarter and more automated to operate intelligently, optimize production, increase efficiency, and be more transparent. This means that it is crucial to take full advantage of the filling units, reduce the risk of downtime and connect, automate and monitor lines, and all this while reducing costs.
-Creating an intelligent factory is not done overnight. Specifically, how can manufacturers approach this issue gradually?-
A report by The Manufacturer * notes that while 67% of UK manufacturers see Industria 4.0 as a whole, only 25% feel that they have sufficient understanding of its implications. That is why we are developing new technology and processes to ensure that manufacturers are ready for Industria 4.0. The first step could be to improve existing solutions. Running a factory in a juggling game between production quality, availability and performance of machinery. To make the most of each of the filling lines, food and beverage manufacturers could consider an integrated solution, which would increase their use and reduce total filling costs. A personalized service contract can also ensure that each of these areas receives the care you need. In this way, the manufacturers can obtain a maximum value and performance.
-What would be the next logical step if these possibilities are explored?-
The next logical step would be to transform the automated technology. Optimizing one or more of the existing filling lines can reveal their hidden potential. Robotics and artificial intelligence, for example, have the potential to radically transform the way we produce. In the market there are machines (1) that allow manufacturers to create more efficient workflows and reduce the hours of manual work. Automatic filling vehicles, which can transport packaging pallets and materials from a central warehouse. This is another step towards the creation of fully automated filling lines. The learning controls adapt the operational, logistical and individual needs of the manufacturers and reduce the visible complexity of the factory.
-And what do you think would be the greatest transformation?-
The biggest transformation would be to make use of turnkey solutions. The Internet of Things (IoT) technology, such as sensors, software and connectivity solutions, can help monitoring and analyzing the productivity of a filling line. By means of these technologies, engineers can conceptualize, design and build complete plants from start to finish that are intelligent, automated and fully integrated. There are monitoring systems (2), for example, which offer a new way to monitor a line, intervene and optimize operations whenever necessary.
-Does this mean that the user has a lot of flexibility when it comes to their own needs?-
Absolutely! The users can view the information of the filling line in different types of pre-configured reports or create their own visualizations. For example, the users can examine graphs that show the OEE, the levels of technical and organizational efficiency, as well as an analysis of the incidents that have slowed down the line. These reports can be seen on a computer, tablet or smart phone, even while being on the other side of the world. Smart notifications alert the team of any incident or problem, and help preventing bottlenecks and stops before they occur. The monitoring system (2) protects the information during the transmission between the machines and the server, as well as during storage. In addition, it provides a permission system that allows the users to define exactly who can access the information.
-What other innovations can we talk about?-
Suppliers of automation and process control systems, such as Manufacturing Execution Systems (MES), work in coordination with present innovative manufacturing solutions for food, beverage and dairy producers. Through these collaborations, advanced production technology is offered. These alliances allow to combine experience for the development of MES products to provide integrated procedures for intelligent and automated factories around the world.
* https://www.themanufacturer.com/articles/
manufacturers-see-industry-4-as-opportunity/
(1) Refer to the Robotic Magazine magazine by SIG –called R-CAM.
(2) Refer to the CombiLink monitoring system.