STAND-UP POUCH: the balance between practicality and convenience
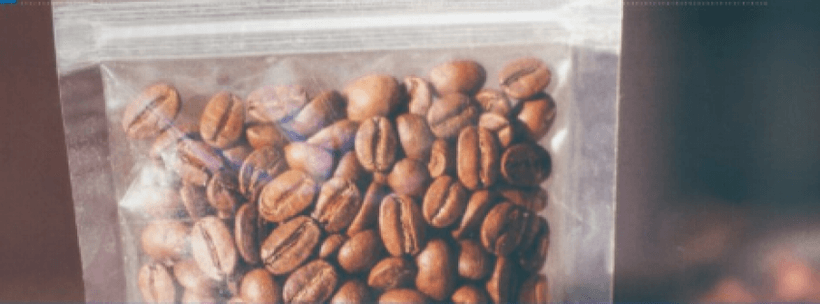
The most sustainable packaging is the one that makes the value chain more efficient with a more holistic approach to the product’s life cycle. A package is not manufactured through thinking of itself, since this would lead to a suboptimization of the complete system. - Claudia Hernández
* Scientific Research and Development of Packaging, Packaging & Specialty Plastics, Latin America, the Dow Chemical Company. Linkedin.com/in/claudia-hernandez-20519118
When a package is manufactured, it is necessary to consider that it will protect and transport the food or other goods, namely from the producer or manufacturer to the consumer. New advances in packaging technology have shown that we can take a major step forward and also consider the recovery or recycling of packaging material after its use.
-Market opportunities and outlook in Latin America-
By 2030, 42% of the total population will belong to the middle class with an increase in the average annual income per household that will be reflected by a larger purchasing power. Each year, approximately 10 million people will leave poverty and become new customers. At the same time, billions of tons of food will be needed to feed more than 1.5 billion people by 2025. All this immediately requires the sophistication of food chains, which are highly regulated, to meet the demands of the market.
-Packaging of new consumption-
Practicality and convenience are characteristics of the flexible packaging that has attracted more and more sectors of consumption. The option that stands out on supermarket shelves in Latin America is the Stand-Up Pouch (SUP) model, a flexible packaging capable of standing up, which allows greater visibility of the brand on the shelf and generates more consumer attention at the moment of purchase. The Stand-Up Pouch, a safe and sustainable packaging, is used for a variety of food products as well as for other consumer items, for example, household products and personal hygiene.
The SUP offers various features, such as the easy open-close system, caps, as well as pouring and directional picks. In addition to facilitating the disposal, the lightness of the material compared to traditional rigid packaging, which optimizes resources in an efficient way upon manufacturing and storage, since less fuel is used during transport of the product to the distribution sites—with more units per vehicle—and since it allows the full use of its content.
Plastic packaging demands a level of engineering that is little known. The vast majority of flexible packaging requires multiple layers, each with a unique function. On an individual level, the resins that make up these layers need excellent control of the catalysts and process variables.
Recent significant advances led to the development and commercial use of molecular catalysts, which also allow control over the polymer structure by way of altering the physical, optical and barrier properties of the final packaging. By modifying the molecular structure of resins and adapting the way they integrate multilayer structures, scientists have developed SUP, a mono-material (polyethylene) or gas barrier packaging, which is fully recyclable (1) and capable of replacing multi-material and non-recyclable equivalents on the market.
-Conventional SUP.-The typical structure of a conventional SUP is a polyester and polyethylene (PET/PE) laminate where polyethylene is typically used to give the properties that polyester does not have.
While conventional SUPs are multi-material packaging, they are practically impossible to recycle. These are leading the new packaging trends as a contributor to the protection of the environment. It is possible to already find a SUP (2) on the market, which maintains the performance of multi-material containers and allows the replacement of more complex structures with an adequate solution for today's recycling processes. And all this is possible without compromising its main function of product conservation, and that in some cases it also allows the increase of the shelf-life of perishable foods.
This type of SUP can pack almost all products and are divided into two categories: with barrier and without barrier.
-Recyclable SUP.- For applications that do not require oxygen barrier, such as frozen foods or dry products. The mono-material SUPs are based only on polyethylene, whether it is a laminate with reverse printing, polyethylene and polyethylene (PE / PE) or a monolamine with direct printing.
-SUP for frozen products.-This category of products, which is widely used, is growing in various food segments, such as pre-cooked and frozen vegetables and legumes, fruits or frozen fruit pulps, products based on animal protein (poultry, perches and seafood). The frozen product guarantees availability throughout the year and convenience to the consumer. The key property required for this application is resistance to abuse.
-SUP for dry foods.- This category of products is very broad and includes grains, cereals, mixtures for cakes and breads, farinaceous products, salt, sugar, condiments. In this group, SUP packages offer convenience for the consumer (open/close system) and differentiation opportunity for the product (visibility on the shelf).
In addition to the resistance to abuse, the requirements for these applications include moisture barrier, keeping the product crispy, preventing water loss (the product does not dry), and preventing water absorption (prevent dust from clumping, for example, salt).
-SUP for construction materials.- The construction materials segment, which traditionally uses rigid packaging (cans, buckets, jars) without the need for a barrier, is gradually adopting SUP packaging. Considerably lighter, SUP is a versatile alternative that differentiates the product at the point of sale. Typical applications within this category include paints, additives and grouts.
-SUP with recyclable barrier.- Even if polyethylene has excellent moisture barrier properties, it does not have oxygen, aroma and other gas barrier attributes. Certain polymers with gas barrier properties, such as EVOH or polyamide (Nylon), are typically used in packaging, but these structures are not recyclable.
The industry has developed a technology of reactive functional polymers of ultra-low viscosity (2), which manages to make compatible polar polymers, such as EVOH or polyamide, by a fine dispersion and incorporate them back into the polyethylene matrix to be recycled or reused. The reactive groups "wrap" the polar components, encapsulating them in micro-domains to achieve an excellent dispersion. Unlike other existing compatibilizers, this new technology not only achieves very good processability, but also an excellent quality film with physical-mechanical and optical properties.
This category includes packaging for cleaning and personal hygiene products, that is, which require a barrier to aromas and also refrigerated prepared foods that demand an oxygen barrier.
-SUP for liquid products.- The segments for liquid products are being specially driven with the Stand-Up Pouch packaging. Cleaning products (soap for clothes, general cleaning, softener): SUP packaging is presented as an alternative with excellent cost/benefit, since it can be used as a recharge and even as a primary packaging (lower volumes/single dose). SUP packaging for cosmetics keeps intact the properties of creams, shampoos, soaps, perfumes and other hygiene items, from production to consumption. In travel, for example, the practicality of carrying smaller containers or sachet is incomparable, mainly in European countries and in the United States, where the reinforcement in security led to the demand for these models. Another important segment is the beverage area (water, yoghurts, flavored juices and some energy drinks): no matter at work, at home, during sports or even in recreational activities, the SUP is standing out and attracting consumers.
The laminated or monolaminated structures (3) present three times more resistance to the perforation compared with the structures of reference of the market (PET/PE). When there is a need for barrier (to oxygen and/or color), the polyethylene structure combined with EVOH still provides a better resistance to puncture.
The seal of the SUP is a critical parameter. Sealing at lower temperatures guarantees a better quality seal (tightness). The hot sealing curves show that the resins recommended for application in SUP are differentiated by a higher strength and lower sealing temperature (independent of the composition with PET and/or EVOH).
Reference: (1) Recyclable in communities with capacity to recycle polyethylene films.
(2) Refer to SUP RecycleReady of Dow.
(3) Refer to RETAINTM, Trademark of The Dow Chemical Company (“Dow”, “DowDuPoint”), or an affiliated company of Dow.