THE DIGITAL TRANSFORMATION as an agent of change
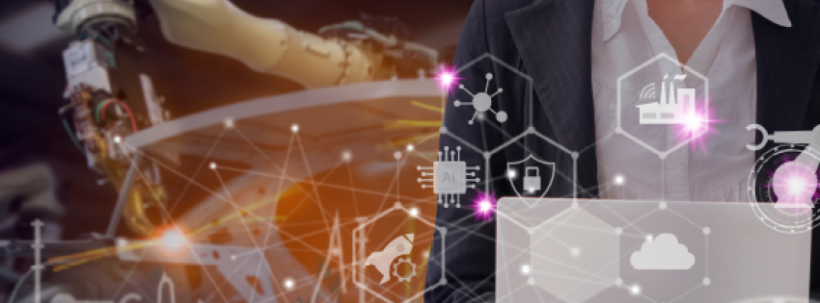
The 21st century is known as the age of digitalization. Globally, in all areas and sectors of industry and institutions, there are more digital platforms and programs that help us to control, streamline and have visibility of the processes, have recent and accurate information, reduce operating costs, share data in real time, and so on. l Erika Grados (*)
(*) Marketing Manager of the Food and Beverage Division of Ecolab Mexico.
Today's digital transformation impacts processes and people alike. Digitalization is already part of the way we interact, work and produce. In this sense, food and beverage processing companies are no exception. In addition to administrative processes, more and more operational processes are being added to the digital age.
Today, the entire process of food generation, from planting to packaging, can be controlled, monitored and measured thanks to digital tools in virtually all sectors. The production, automation, monitoring, transport and sales processes have been directly impacted by the technology.
If we compare methodologies used ten years ago (a period not too long, not too distant) we can see that although the essence is the same, the efficiency is much higher, as are the quality standards, in contrast to the times that are now shorter.
There are numerous benefits within the plant:
- Making the operation efficient
- Ensuring the product quality and safety
- Have visibility and control of the process
- Cost reduction
- Safety for operators
- Generate operational savings, standardization, among others.
In short, producing more while taking care of the final product at the lowest operational cost, so it becomes more critical every day to have a digitized operation.
In addition to the company's own process, it is also important to consider external tools that help in this digitalization, i.e. technologies, applications or software, where input suppliers also have a way to be monitored and controlled through some platform or digital media.
The digitalization of the manufacturer and its direct and indirect suppliers will strengthen the operation, maximizing its efficiency and reducing its cost. The visualization and control of the whole process in real time can avoid many headaches and significant economic losses, in addition to caring for the brand, which is invaluable.
Also, with the help of digitalization:
- Reprocessing can be avoided
- Stop any harmless (or off-spec) product before it goes to market
- Reduce water and energy consumption
- Ensure proper cleaning and disinfection of equipment and surfaces
- Maintaining the correct process temperature
- Monitor the indicated concentration of the chemicals
Dairy sector makes way for technology
There are thousands of examples of the applications of technology and digital tools in this industrial age. But how can we use technology to ensure products that exceed all standards of taste, quality, safety and also save resources and have an optimal process?
One of the answers would be: to have eyes on all parts of the process and in case of contingency to take the relevant and timely decisions. That's where technology comes in. When it is impossible to have a person inside a pasteurization tank, for example, devices can be placed that report changes in temperature or the presence of some substance that compromises production excellence. Technology can be where a person is not, and provide information to those who solve problems and make decisions.
Another example in this same industry would be the dryers and evaporators, two of the most energy-consuming equipment, elements whose correct operation is vital to reduce costs and comply with the specifications of each product, so using technology to make their performance efficient represents a significant advance.
Real-time monitoring
Suppliers* understand the challenges and concerns, so they have technology that can help in the quality assurance of the final product. Imagine how one of the most critical issues in the process, such as cleaning and disinfecting surfaces and equipment, can be monitored in real time and be visible to all previously defined personnel.
What would it be like to have visibility of all CIP (Clean In Place) cleaning, would it be useful to share in real time not only the results of the cleaning but also the cost behavior associated with it?
Plant managers or senior staff can now have real-time visibility of cleaning data from all their CIPs across their company's plants, so they can maintain corporate standards, ensure KPI compliance, avoid financial loss and optimise their operating costs.
The 3DT CIP* technology is an example through which it is possible to monitor, detect and control the CIP process in real time, thus achieving through a digital platform, total visibility of the process, ensuring the quality and safety of products with more efficient, safe, productive and sustainable operations.
Ensuring consistent cleanliness at all levels - microbiological, physical and chemical - is a task that requires extensive knowledge. For example, 3DT CIP identifies and solves a number of problems in a cheese and other dairy production plant, including fixing a leak in the heat exchanger valve, reducing cleaning times and optimizing chemical consumption.
The combination of technology and personalized service helps the plant save nearly $34,000 in energy costs, improve food safety through early identification of 1,800 emerging issues and reduce washdown times by more than 2,000 hours, in addition to reducing total costs by $244,000.
On the future of technology, there is still much to be advanced, discovered and innovated, however, it is likely that the digitization of this new industrial era will change the way production processes evolve, that automation will have a greater reach or why not, that artificial intelligence will take over entirely the processing and safety of food. The possibilities are virtually endless.
Issues such as Cloud Computing or Big Data, two of the tools with great potential in the medium term, will allow the management of high volumes of data, which will provide ease of use and customized functions, free access at any time from anywhere, information security, constant updating and, consequently, cost savings.
What should not be lost sight of is that the end user is the important part in the whole process. Today, consumers expect foods to have minimal processing, additional value and high nutritional qualities, so designing methods and processes that maintain and enhance these characteristics must be one of the primary parameters in all product processes.
* Refer to the 3DT CIP technology from Ecolab, a multinational company that contributes to a cleaner, safer and healthier world by offering comprehensive solutions and on-site services that promote food safety, maintain clean environments, optimize water and energy use and improve operational efficiency.