Sustainability and Recyclability of Flexible Materials for Primary Packaging
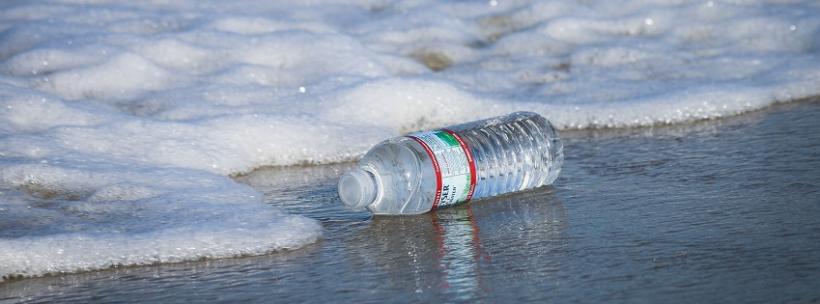
Innovative film and their relations to flow pack machines
Author:Lorenzo Birro
Source:www.biscuitpeople.com
The perception of the Consumers has drastically changed in the last years. Plastic packaging yesterday seen as a friend to protect the food and reduce food waste, nowadays is seen as an enemy for its environmental impact.
The emotional approach to the matter, mostly handled through the Social Media, is quite strong and it drives towards an even stronger request of a PLASTIC FREE WORD.
The very strong pressure from the Consumers on all players of the Supplying Chain (from the GDO, through the Packaging materials Producers and Converters till the Wrapping Machines Manufacturers) is forcing them to search solutions where traditional plastic can be replaced, reduced or at least made recyclable.
However, it must not be forgotten that the main objective of food packaging is the protection and preservation of the product. Plastic is definitely one of the best materials to obtain the desired results in terms of “shelf live”. Presently about 1/3 of produced human food gets lost or wasted (FAO digital report 2019). Bad packaging is one of the main reasons.
It is unthinkable to renounce to plastic at least in PRIMARY PACKAGING; but there is no doubt that it can however be reduced, recycled and in particular situations, replaced with paper and other biodegradable films.
All companies involved in packaging must consider and take in serious consideration the challenge to protect and preserve food offering in the meantime solutions to reduce the Ambiental impact.
Among them, certainly, Cavanna - a leading worldwide manufacturer of flowrapping and cartoning plants - is one of the more active and attentive in such issues.
The Cavanna made lines produce every minute an average of 1.2 million of flowpacks and therefore Cavanna has a kind of moral obligation and responsibility to be involved and to develop solutions to dispose such huge amount of packs.
To do so, Cavanna has created a new Business Unit called TCO CONSULTING with the aim of dealing with the changes in wrapping materials following the GREEN ECONOMY topic. One of the tasks of the new TCO CONSULTING structure is precisely to create a network of contacts able to find innovative wrapping materials and bring them to Company R&D Division to be practically tested in Laboratory to evaluate the performances of the machines in terms of speed and seal quality.
The Consumers pressure and the Official Directive regarding circular economy has brought to two main areas of intervention on primary flexible packaging.
A. RECYCLABLE PLASTICS
RECYCLABILITY is the path chosen by Europe and USA to tackle the problem. The above will bring important changes to the materials that must be as pure as possible (and this means not polluted by other plastic families) to promote separation and recycling.
What was used until yesterday may no longer be used by tomorrow:
- The mono-materials (PE only, OPP only) will grow at the disadvantage of the typical multi-materials structures such (laminated PET + OPP, PA + PE, etc….)
- Cold sealing is expected to be replaced and reduced
- The triple ALUs structures, typical of the pharmaceutical and the coffee industry, will no longer be acceptable
- Paper laminated with renewable bioplastics will considerably increase
As one of the leading machine manufacturers Cavanna could not be caught unprepared for these changes which could lead to important changes even in crucial parts of the machine.
Innovative mono-materials are expected to influence machine performance in two areas:
- Sealing: innovative mono-materials are generally more sensible to temperature than previous complexed films. They need more precise temperature intervals (smaller working windows).
- Sliding: very often these films have different Coefficient of Friction (C.O.F.) and they might require the use of special sliding coatings in dedicated machine areas.
B. BIO-PLASTIC FROM RENEWABLE SOURCE
They are plastic materials that could be biodegradable, bio-based or with both characteristics (European bioplastic definition)
With the name Biodegradable we mean a material subject to microbial degradation while Compostable is a biodegradable material under certain precise conditions of time, temperature and humidity. In terms of volume they represent nowadays around 0,5 % of total plastic packaging.
Biofilm are coming from renewable source and are produced by polymerization of natural bio-monomers mainly from starch and/or cellulose. Most common families are: PLA (Polylactic Acid) - Starch Based and Cellulose Based with a great variety of options and grades. Normally cannot be used as mono-film in the flowpack machines and need to be laminated with film that offer thermic stability and anti-sticking properties. Paper, a natural biopolymer is often chosen to be laminated with other biopolymers and is ideal for its biodegradable characteristics and thermal stability.
All bio-film families have few main points in common
- Are Biodegradable and Compostable
- Are cost effective: 3-4 times more expensive than plastic materials
- Bring to and increased total thickness of the film itself
- Have generally poor barrier to moisture and oxygen
- Have reduced production volumes
- Are thermally less stable
From machine performance point of view the bio-film families will receive even more attention than the mono-material for R-Plastics. Sealing areas and slides surfaces are in processing to be re-studied and modified to suits to the characteristics on these innovative films.
Cavanna final goal and target is to present to the market a GREEN KIT made by few sensible parts and adaptable to existing machines to challenge the working performance of the innovative film without compromises in speed and seal quality of the pack.
Leading photo by Brian Yurasits on Unsplash