Profitable PET line FOR WATER BOTTLES
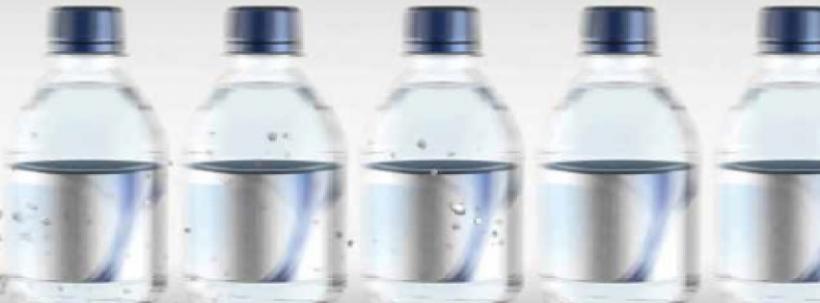
In recent years, the production and consumption of bottled water has grown to two digits. Whether directly or indirectly, PET bottles reach the filling groups to excel in a more sustainable market. l Nadia Perera*
* Editor at Contenidos.
The company Abant Su has become one of the main mineral spring water-bottling plants in Turkey. In order to continue to expand and to be among the three best suppliers in the medium and long term, the bottler chose the water technology and service KHS.
Since 2008, the Turkish company has successfully marketed spring water under the Abant label. The company, which is part of the Kaya Holding group, has constantly been expanding its production facilities. In 2015, it opened a second production site in Gölcuk at the Mamara Sea east of Istanbul.
The company has now become a new stationary bottling line, which was built by KHS. Kaya Holding, CEO of BurakKaya, explains that they opted for the modernization of their technology so as to provide a better quality of packaging and to improve the efficiency of their production lines, since they are as important as the purity and taste of their product.
Abant Su wanted a particularly compact machine, which was perfectly adapted to their specific needs. The KHS* line provided a slightly smaller stretch moulder equipped with 18 instead of usually 20 to 22 stations. At the same time, production increased from 2,250 to 2,500 bottles per cavity, resulting in a total system capacity of up to 45,000 bottles per hour.
Another advantage of the new line is that it allows for saving more energy. The system uses around 30% less electricity compared to other technologies. It also uses up to 40% less compressed air. The 0.5-liter bottle weighs only 9 grams and is currently the lightest on the market in the region. Moreover, it requires 10% less material.
Efficiency throughout the process
The packaging line has a labelling and a packing machine that ensure that Abant PET bottles are not contaminated by dust, which helps to reinforce the image of purity of the brand. The packages also remain stable during transport.
The system is a station of labels by means of rollers, which apply a layer of gumming on the bottles to later place the labels. This type of solution can be used with films, aluminum foil or paper labels in unidirectional, cylindrical and rectangular containers.
The label material goes from the reel to the labeling station, where it is cut to the exact length. The cutting system is optimized with self-sharpening blades, which offer a high operational reliability and a higher cutting precision. The team can label up to 50,000 bottles per hour. What has represented the Turkish company is that it saved time and money thanks to the correction of their labeling systems.
The company Abant explains that the market demands a robust, but attractive secondary packaging, which is profitable to produce and also has a sustainable aspect.
For the brand, the packaging of its bottles is of the utmost importance, since it is not just the material playing an important role, but so does the presentation of the packaging, which is now of great importance in order to reach a greater number of consumers. The system saves resources, since the corrugated trays and pads, which were previously used to stabilize the package, are no longer necessary.
With the application of the system, the bottles can no longer move within the package, packing line, transportation, or at the time when consumers are buying the product. Another feature, which buyers viewed as being favorable, is that the packaging has a handle so the transportation is easier and more convenient.
The changes in its production have allowed the company Abant to reach better results and to reduce the costs in the entire packaging line.
Innovations in the PET packaging line
In order to meet the growing demand of its customers, the British company producing natural mineral water, Montgomery Waters spring, acquired a second solution of a packaging line for PET bottles. The firm opted for the Sidel Matrix equipment.
The company, which is based in Wales, has several sources dedicated to the supply of gaseous or non-gaseous water, flavored and enriched with vitamin, under its brands Aquaroma, Celtic Spring and Aquavit, and it also bottled for other manufacturers. Among the firm's customers that are part of the British bottled water market—with a volume of two billion Euros—there are several leaders in the retail sector, sports club chains and hotel establishments throughout the United Kingdom.
Paul Delves, executive director at Montgomery Waters, explains that they started blowing their plants and updated the labeling operation in 2012 by way of modernizing the high-speed line, which increased the production capacity by 50%.
"A greater demand on the part of both consumers and our customers implied the need to invest in a traditional line, which offered a maximum capacity of adaptation and could be integrated into the solutions we had already installed, so as to provide flexibility to operators in all our lines and to reduce the training needs and maintenance costs," the executive explains.
Experts of the solution state that the choice of a complete line solution for PET involves much more than the sum of its individual parts: it covers everything from the concept of packaging to the process of equipment, the design and supply of the line, the productivity management analysis, and the continuous attention for improving the line’s performance. The planning of the complete solution must overcome the challenges of the supply chain with the implicit permanent goal of achieving the lowest cost of ownership.
Therefore, the machinery is equipped with a Blendfill version of the Sidel Matrix carbonator, which means that it uses a single intermediate tank and allows for a reduction of the CO2 consumption. The 70 filling valves are equipped with electronically controlled flowmeters so as to ensure a precise filling volume inside the PET bottle, and thus to prevent spills and waste of the beverage.
The labelling machine is a modular coil machine, which can be installed in many different arrangements and which can easily be reconfigured. The times of format changing are 30% faster than previous generations of labelling machines, while stoppages in production due to maintenance are 40% shorter.
Once the line was installed, the performance was at 90%. The layout and problem of limited space was redesigned by installing an automatic storage system for preforms. The two-liter bottle line operates 24 hours a day and seven days a week during the peak production season.