FLEXIBLE PACKAGING LINES in response to new demands
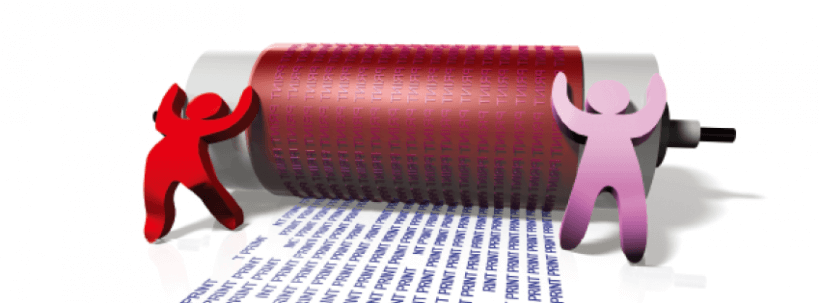
Given the demand for a wide variety of packaging, optimal planning is necessary to generate feasible, predictable packaging with low processing costs, print quality, brand consistency and great impact on the consumer: achieving transformation and tangibility from the digital world to the final physical packaging. l Patricia I. Christensen (*)
(*) Business Developer of SGS.
The main objectives of the Consumer Packaged Goods (CPG) are:
1. Physical-mechanical functionality. A packaging with high physical-mechanical functionality will guarantee high levels of productivity in the filling lines, the integrity of the product for the time of its life, as well as an optimal handling in the transport and storage.
2. Brand uniformity. One of the main marketing objectives is to maintain consistency in the creation of the original image concept to market your product and make it attractive through the image achieved on the packaging.
Having therefore the conceptualization of design/branding with printing feasibility as a premise, it is essential that the process of centralized graphic and prepress production is carried out properly, with the aim of:
- minimizing the pre-production, graphic production, print and post-production steps of brand continuity.
- eliminating the duplication of processes where a graph is generated individually and then distributed in several channels, which in an isolated and different way generate their own flow producing divergences and inconsistencies within the same printing method and even more between different printing processes.
- cost reduction. Once the graphic is centrally managed, the preparation and development of the packaging is done once, with the adaptations of each process output, but always maintaining the image uniformity in the graphic generation stage at a digital level.
3. Speed to market. The centralized prepress model will be the main support to achieve the key points of interest of the CPG, having as final result:
- process efficiency.
- cost reduction.
- uniformity and consistency of the brand.
- Opportunity for market impact by accelerating product release in a shorter period of time.
In the production process it is essential to foresee how the product will look before it is printed. This process starts with the print feasibility analysis. For this item, the following is necessary to be considered:
- Available printing technologies.
- Reproduction capacity and ranges possible to achieve with the printing tools, offset, rotogravure, flexography, letterpress, digital printing, etc.
- Measurement and control of processes. This leads us to obtain consistency within each process once an acceptable result has been achieved for each technology.
- Evaluation criteria by the CPG at the time of receiving the package on the graphics achieved in production.
When production standards are available and the process is finished, the CPG creates the evaluation criteria for an objective evaluation of the color reproduction of the packaging: color standard applied to the profiled target in the printing process; color measurement equipment and its calibration; tolerances and measurement ranges, and measurement method and target values for both color and tonal ranges.
For a good result in production it is very important during the design phase to create art with the end use in mind.
The recommendation
Centralized management of the prepress process and color management in packaging production ensures brand consistency on packaging substrates and printing technologies:
- Workflow considering production feasibility, print technology, color management from design to print
- Digital graphic development management systems where the different parts of the process flow interact: packaging user, design agency, pre-press process management agency, printer.
- It is fundamental that the centralized pre-press process management agency supports the brand managers and packaging suppliers by providing its expertise and aligning all parts to create the best possible results, characterizing printing processes and generating color profiles where the printing processes interact and are homologated with the different substrates where the packaging will be produced.