Effective medical device packaging standards for sensitive devices
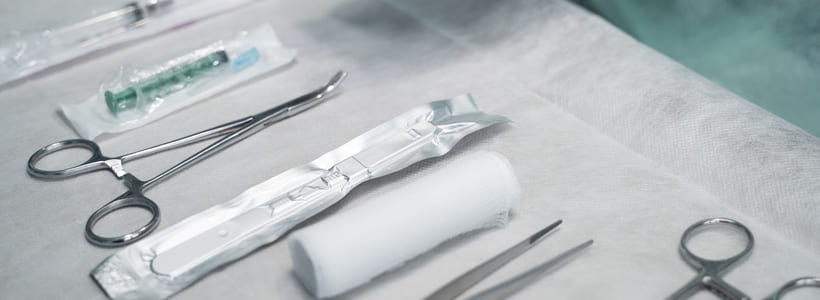
Medical professionals regularly use sensitive medical devices to treat patients — even save their lives. But those devices don’t simply materialize. They arrive en masse to hospitals and physicians’ offices having traveled great distances while encountering sometimes adverse conditions. That’s why packaging is so important.
But it’s not without challenges. With sensitive medical devices — such as pacemakers, catheters, and implants — almost anything could go wrong. Let’s take a closer look at some of the most important considerations medical device manufacturers need to make with medical device packaging and the care sensitive devices require.
The Critical Role of Packaging in Healthcare
Devices that may save a person’s life or be surgically implanted in their bodies can’t merely be wrapped in plastic and shipped without second thought. A solution that minimizes the risk of contamination or damage is vital.
Sterilization is key, as is device stability. These devices are often engineered to strict specifications to match the human bodies they’re meant to help, and the packaging must be engineered just as carefully. Patient safety depends on it.
Preserving Precision & Accuracy
Delicate medical devices are designed with exquisite detail and precision. The packaging must protect the devices against contamination, tampering, and electronic interference that could alter the calibrations of the device in any way.
All areas in the packaging must be as exact and precise as the device. The material composition itself, the thickness, the flexibility, every curve, every crevice — it must all be carefully calculated to maintain device integrity.
Challenges in Packaging Design
Packaging is the first line of defense for medical devices. Contents must be kept sterile throughout the process, and the packaging must offer barrier protection against: moisture, heat, cold, sunlight, chemicals, electronic interference, radiation interference, bacteria, mold, dirt… essentially, everything. Everything that could contaminate or compromise the device must be kept out. People’s health and lives are on the line.
The packaging must also be strong enough to withstand shipping, movement, and storage conditions. These packages may move around warehouses and different transport vehicles often before arriving at their final destination.
Strength, precision, barrier protection — it’s all a challenge. But it’s all doable.
Customizations for Device Variability
Medical devices come in various shapes, sizes, and have different functionalities, so it’s vital to have custom packaging solutions that adapt to each device.
Some of the most common packaging methods are form fill seal, thermoforming, and pouches. Form fill seal packaging, for example, involves forming a package, filling it with the product, then sealing it. Thermoformed trays, on the other hand, mold rigid plastic into the shape of the device for the kind of protection sensitive medical devices often need.
For as many medical devices in existence, there are almost as many ways to package them. This is why working with a partner such as Amcor is ideal; as a device manufacturer, you’ll have access to the materials, engineering, design, formats, testing, and expertise that allows for tailoring packages to the specific requirements of virtually any product.
Regulatory Compliance
Another top concern is ensuring compliance with all FDA and other regulations. The FDA’s Title 21, Volume 8, Section 820.130 regulation advises that medical device packages must protect the devices “during the customary conditions of processing, storage, handling, and distribution.”
The medical devices themselves often have their own strict expectations and regulations. The packaging must prevent damage and any other possible contamination or interference that would compromise the device and render it unusable.