Challenges of INDUSTRY 4.0
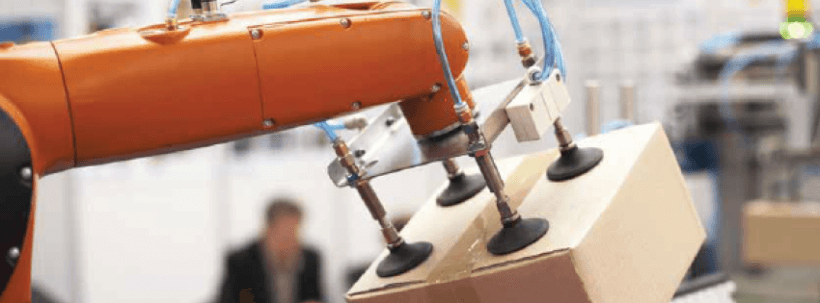
The digital transformation 4.0 or the Internet of Things (IoT) are gaining momentum. Numerous applications of the fields of product and process monitoring, labeling technology, packaging, logistics, maintenance and repair nowadays are manifesting the potential for optimization, which is involved with the Internet of Things. l Hans-Peter Fritsche*
* Professional journalist at Interpack 2017 – linkedin.com/in/hans-peter-fritsche-6558ab75
In the future, sensors, chips, RFID (radiofrequency identification), equipment, machines and plants are not only expected to address information on all important process and system conditions in an independent and continuous manner, but also to communicate between them through the Internet, and intervene in manufacturing processes in order to correct and optimize them without human intervention.
The basis of communication on the web is the Internet Protocol (IP) with its unique identification IP addresses. However, the old IPv4 was only able to offer a space of just under 4.3 billion IP addresses. This is the reason for its development to the new IPv6 standard, which has a space of 3.4 x thousand 38 IP addresses. So the lack of space is no longer a concern. Therefore, the challenge is the flood of data caused when billions of sensors on a day will be transmitting thousands of data per second. These data must be evaluated for visualizations and simulations, and saved for documentation purposes (traceability).
So to be precise, the IoT is principally based on data, on the information retrieved from them. And this is the domain of software and algorithms. What can be achieved with this must be enough reason to actively promote this transformation. The following examples show the applications achieving their short-term objectives.
Change in the paradigm of maintenance
Damaged transmissions, pumps or filling and dosing systems give no warning until the problem is already present, but "give notice" long before the damage is caused by unusual deviations from vibration and temperature or by changes in the power consumption, loss of pressure, and similar. These deviations detected by the sensors can be evaluated and visualized in real time due to highly complex analysis and simulation programs, and therefore it will be seen in the context of process engineering.
Based on this information, the operators of machines and plants can selectively intervene in the system by remote control and, above all and regardless of the location, introduce any changes in the program or install new applications and control software in order to always execute the systems in the optimal way. In addition, the results of the simulation allow precise forecasts on the remaining useful life of the machine’s critical parts, which opens completely new perspectives for maintenance.
This means, we are moving away from both the reactive and preventive maintenance with its component replacement intervals, which are based on cycles and going towards predictable maintenance measures up to the so-called predictive maintenance.
The advantages are a greater availability of machines and plants, a substantial reduction in downtime risks, an increased operational and production safety, as well as lower investment costs in maintenance.
Beyond this, predictive maintenance is a key element in sustainability. In fact, operators have always replaced the components at fixed intervals, but also wasted the useful life of the remaining and expensive components because they lacked reliable data on the behavior of the parts.
Chatting with machines
The increase in performance, flexibility and intelligence of machines and plants is increasingly complex, and poses greater challenges for concept developers in the operation of human-machine interfaces (HMI).
A central aspect in the development of graphic interfaces is to ensure that these machines can also be operated safely by people who do not have any professional training and lack a sufficient linguistic knowledge.
In order to avoid operating errors, GUI developers rely on intuitive graphical elements instead of language. Moreover, photo-realistic 3D CAD screens of machines, plants and components are presented. In addition, the HMI has to be up to the needs of several users according to their abilities so as to ensure an easily understandable visualization and an instant presentation of the key parameters of the machine and the production data.
There is a tendency towards mobile devices, with which the user can remotely control the machines and equipment depending on their level of authority. This saves time and travel expenses, especially in the field of service and maintenance.
Working in virtual worlds
When it comes to the IoT, there is hardly one issue currently causing a stir as virtual or rather digital twins. The technical basis of these are high-performance CAD 3D graphics, simulation and analysis, as well as virtual 1:1 copies of real software for controlling the machines and equipment. Based on these software tools, the digital twins map the entire manufacturing process, including components, machines, plants and their controls as a virtual model (complete with all the physical data required for the simulation). In addition to this, digital twins enable the offline programming. All this makes them universal tools for developers, operators and maintenance personnel.
Thanks to these simulations of near reality, design errors and/or weak points can already be detected and eliminated in the development stage without having manufactured a single real piece in advance. This also applies to the programming and optimization of controls.
The digital twin is the flight simulator for industrial processes, machinery and equipment. The virtual pre-boot before the actual start-up is worth it in more than one way. In case there are still errors in the system or concept of control, they can be remedied without compromising the components of the real system. In turn, the offline programming enables production planners to virtually test various modes of operation. However, the most important aspect is that the virtual twin brings the experience of many specialists who can then be used for other projects.
In short, thanks to sophisticated simulations, manufacturers and users of the plant can achieve significantly shorter project execution times, faster starts and considerable efficiencies in the development of similar plants and processes. This saves time, but above all, resources, energy and manpower.
The old systems are able to handle 4.0
Numerous old machines, lines, motors and compressors are not equipped with sensors and communication technology for Industry 4.0. They are sometimes not even able to operate as part of networked systems. However, this does not mean that they are obsolete in view of the digital transformation. Smart sensors can be adapted here as an entry-level solution for Industria 4.0. These sensors regularly measure important condition parameters of the machines and systems, and transmit the data through communication interfaces, which are wirelessly integrated in the employees’ HMIs or in smartphones or tablet PCs for their evaluation. With these and other simple methods, companies can enter the world of Industria 4.0 at no high costs, and continue to benefit from reduced downtimes, longer machine run times as well as from lower energy consumption, etc.