Challenges in the machinery for THE E+E INDUSTRY
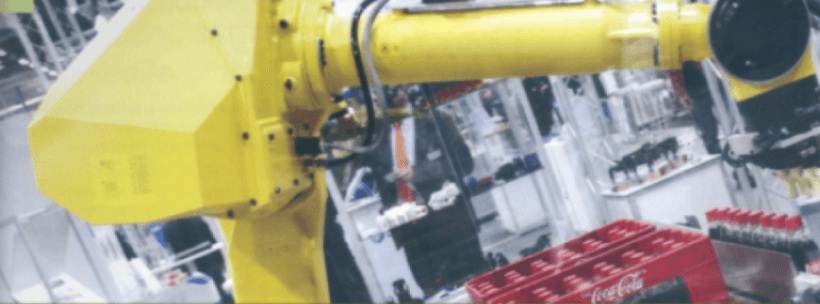
By taking advantage of the new digital strategies provided by technology, the main food and beverage companies have managed to improve the uptime and performance of their processes. * Madia Perrero*
* Content Editor at Énfasis Packaging.*
According to the latest data from the research agency LNS Research, two of the three main strategic objectives for food and beverage companies are to ensure constant quality and the increase in the production capacities to meet the growing demand.
On the other hand, limited budgets for capital expenditures mean that these objectives are ideally meeting the existing equipment.
Operating under these limitations, it is critical that brands use the tools at their disposal to optimize the availability of assets in order to boost the maximum production and to maintain the quality.
-Trends in technology for A&B-
One of the most important trends we have seen in food and beverages is an increasing demand for end-to-end traceability, and there is no indication that this trend is slowing down.
The consumers nowadays wish to have a better clarity about the origin of their food, and where it has been at each step of the trip. They want to know which farm was delivered with what kind of raw material, which plant processed it, and how the finished product were brought to the supermarket.
A continuous demand for clean food is expected, this means more variations in the products and in the containers, which will surely affect the existing equipment, systems and manufacturing processes. Brands must improve their manufacturing agility with tools, such as the digital administration of recipes, and the integration of the supply chain to keep up with the consumers’ changing demand.
Digital transformation and end-to-end integration of the supply chain allow for a comprehensive traceability that consumers, retailers and regulators wish for.
Cloud solutions are becoming more frequent in manufacturing operations. New security standards, offline performance capabilities, and centralized management visibility can provide a new flexibility and scalability while the total cost of ownership is maintained.
This is ideal primarily for manual or semi-automatic operations that require minimal local control, and it is especially effective for plants located in remote locations or geographies, where limited local support staff could mean long delays due to unforeseen equipment downtime or malfunction of the system. A hybrid approach is the most flexible implementation model.
-Digital transformation in A+B-
Food and beverage manufacturers can take advantage of the Industrial Internet of Things (IIoT) to move from a reactive to a proactive maintenance model. This change can have a dramatic impact on the profitability, allowing (by allowing) assets to become facilitators of greater profitability rather than simply being a cost center, as detailed in the study: Robotic applications for the packaging industry, by Technavio.
The implementation of digital transformation in asset management adds a critical context to industrial macrodata, allowing users to derive actionable insights that can be used to improve the asset performance and reliability.
At the most basic level, a data historian provides a detailed view of the time series and the historical data of the assets, which allows a real-time view of the past problems. The next level of maintenance maturity is condition-based monitoring, which allows for a more proactive approach.
In the supervision based on the condition, the user establishes the logic based on the rules. Infractions, such as equipment operating hours and limit violations, can automatically trigger work orders.
Predictive maintenance is ideal for high-cost mission-critical assets where unscheduled downtime would cause a serious impact on the business. These solutions use advanced analytical techniques, such as advanced pattern recognition and machine learning, to detect any problems before they become operational.
Early warning notifications are activated days, weeks or months before any deviations from the reference point appear, allowing the staff to better plan maintenance activities and avoid costly failures.
Maintenance capabilities focused on strategic reliability allow a risk-based approach by allowing users to plan and simulate their strategies to determine their long-term impact. This, in the end, helps improve the reliability and repeatability of the maintenance process and facilitates continuous improvement, which enables plant operators to spend less time analyzing data and more time to take action. As with operations, the model-based approach allows the development and adoption of best practices for maintenance throughout the business, improving efficiency in the manufacture of food and beverages.
The study highlights that these benefits are more than theoretical: the major food and beverage companies are using these concepts today to improve the reliability of assets and to maximize the efficiency. For example, New Belgium, one of the largest craft brewers in America, needed to increase production using its existing assets.
By implementing the digital transformation in all its operations with an MES, the New Belgium staff was able to see detailed information in real time about any unscheduled downtime. As a result, the brewery reduced this time by more than 50%, which increased the overall effectiveness of the equipment (OEE) from 45% to 65% in just over two years. This improvement enables the brewery to expand production from 150,000 to 200,000 boxes per week without additional capital investments.
-The main transformations contributed by data reading-
Specialists from LNS Research analyze that when studying the impacts of industry 4.0 in the food production chain, one of the factors that always stands out is the traceability of the entire process. That is, the possibility of monitoring, recording the conditions of production, transportation, and conditioning of food; telling the full story of his from the source to the supermarket gondola.
Measures to implement the concepts of industry 4.0
Production automation.
Interoperability of all sensors and systems in an industrial environment.
Process virtualization.
Adaptation and production in real time.
Modular systems of equipment and production lines.
Decentralized production processes.
This means that new technologies for reading data in Industry 4.0 will allow to obtain and monitor all the information in a much more accessible and fast way.
The advantage of reading data is enormous. As they permeate the entire production chain, these technologies allow an improvement of the food quality, avoiding waste with transportation and storage, it is contracted, and bottlenecks are identified throughout the process. Therefore, there is a more effective control of all the variables that now cause food loss.
Industry 4.0 also makes it possible to carry out the planning and programming of the production as a whole. For example, it is possible to use the Cloud to combine data from the brand with those of suppliers and customers in real time. Thus, everyone can collaborate to generate more assertive results that meet market demands.
The data allows a much greater understanding of the needs and tastes of consumers. By means of a good crossing of this information, it is possible to identify patterns, to accompany the levels of customer satisfaction, and to offer increasingly personalized products.
-Importance of smart packaging-
New technologies help to avoid waste in companies, because they facilitate the handling of products and reduce problems related to packaging and food preservation, the Technavio study points out.
Smart packaging will act directly in the conservation of food with the emission of protective substances or devices for the absorption of others that accelerate the degradation of a perishable product.
With these containers, it is possible to better face the problems of proper food preservation, since they enable better logistics in relation to it, and facilitate the entire process of the distribution of food and beverages.
The use of the 3D printer in the production of small batches of an exclusive production facilitates the manufacture of customized packaging with lightness and design.
Using new technologies allows to identify the conditions of the packaged product without the need to open it. Smart packaging acts in the monitoring of the content showing and regulating the temperature and humidity conditions. It becomes the key that contains the memory of the final product.
The implementation of Industry 4.0 allows for significant saving by way of having a product, which will contribute to the improvement of various aspects related to the food industry, from the packaging process to the distribution and delivery of the product to the final consumer.
The greatest impact for the industry is related to the reduction of costs, taking into account that the sensors of the containers are produced with low-cost materials and provide great benefits, such as reducing the waste of the product.